Kiln Design and Construction for Natural Wood-ash Glazes
Design, construction, and firing of a traditional ceramic kiln with natural wood-ash glaze as decoration.
Makoto Hatori's traditional climbing kiln has a firing temperature of 1200–1300 and a firing period of 8–10 days. Inside the kiln, there are various states of oxidation and reduction. These conditions, the atmosphere inside the kiln, are the conditions that produce 窯変 yohen "kiln transformation (accidental coloring or glazing by flame)." This record documents the firing process inside the kiln.
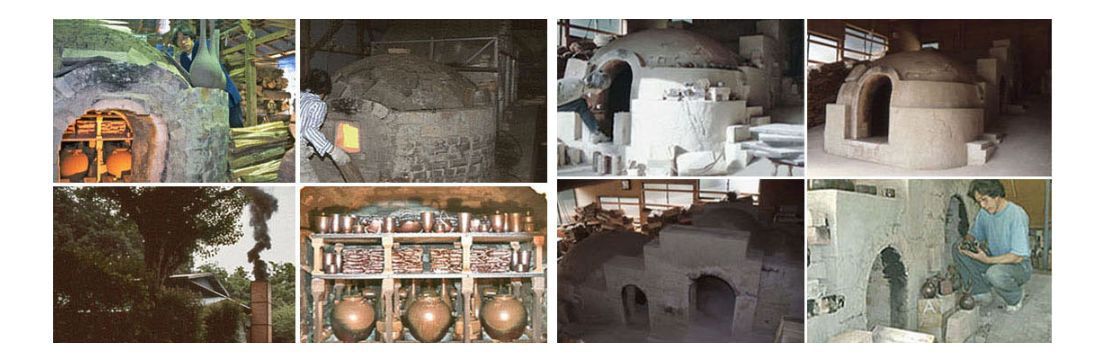
The Bizen ware climbing kilns, designed by Makoto Hatori himself, were constructed at different times. The kiln on the left was built in 1978, while the one on the right was constructed in 1995. Notably, Makoto Hatori personally constructed the kiln on the left.
In the video "Kiln, Clay, and Form," Makoto Hatori introduces the unique and traditional process of firing ceramics in his kiln, loading kiln and filling kiln techniques. During the Momoyama period (late 16th century), when Japanese ceramics reached their peak and villages had a lifestyle blending farming and pottery, potters worked in groups and used a single big climbing kiln called a "noborigama" They would commence firing the kiln around the time of the first snowfall and reportedly unload it when cherry blossoms bloomed. This was necessary due to the clay's exceptionally low fire resistance, which served as the base material. As a result of the extended firing period, the vessels inside the kiln would become covered in firing ashes and adorned with various unique decorations. In the video, contemporary studio ceramic artist Makoto Hatori demonstrates the traditional kiln firing and loading process.
In Makoto Hatori's studio, this climbing kiln was fired twice a year for roughly 10 days at a time. The entire procedure, which is done using conventional techniques, is shown in the film that was presented here, from firing through unloading the kiln. The final step, known as "ootaki," in which a substantial amount of wood is put into the kiln, is repeated numerous times, as seen in this video. This is a significant procedure when the vessels are given as much natural wood ash glaze as possible. This video was created in 2018 using resources from the time period.
“The Process of Building the Kiln" presents a step-by-step guide for constructing a kiln. This document depicts the process of constructing a traditional kiln, which took place between May and August 1995. "Makoto Hatori's Kiln Drawing" was published on page 229 of "Wood-Fired Ceramics: 100 Contemporary Artists" by Amedeo Salamoni, with a foreword by Jack Troy. The book was published by Schiffer Publishing, Ltd., located at 4880 Lower Valley Road, Atglen, PA 19310, USA, and was released in 2014.